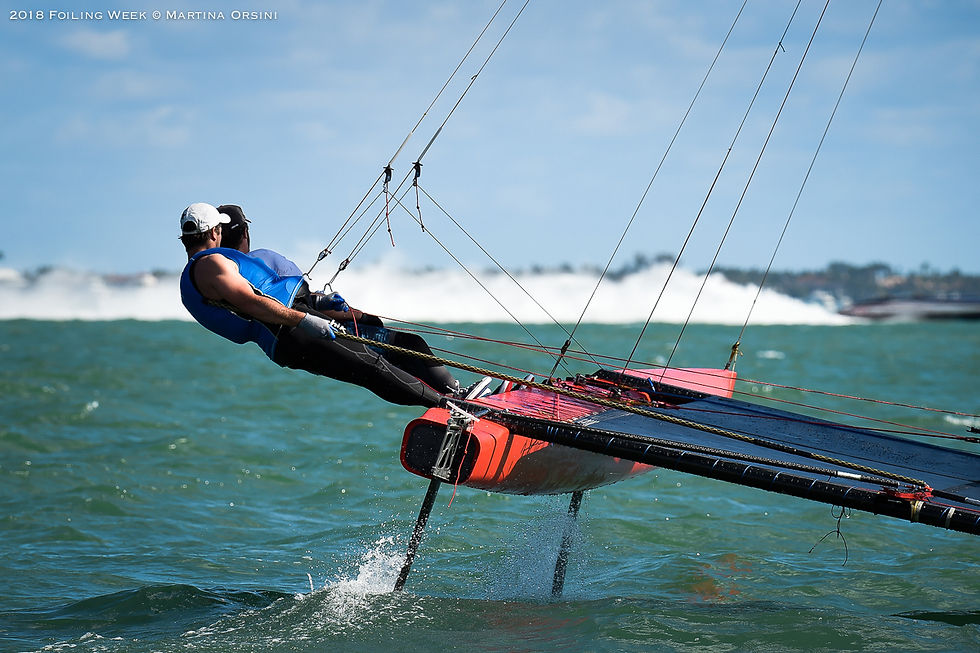
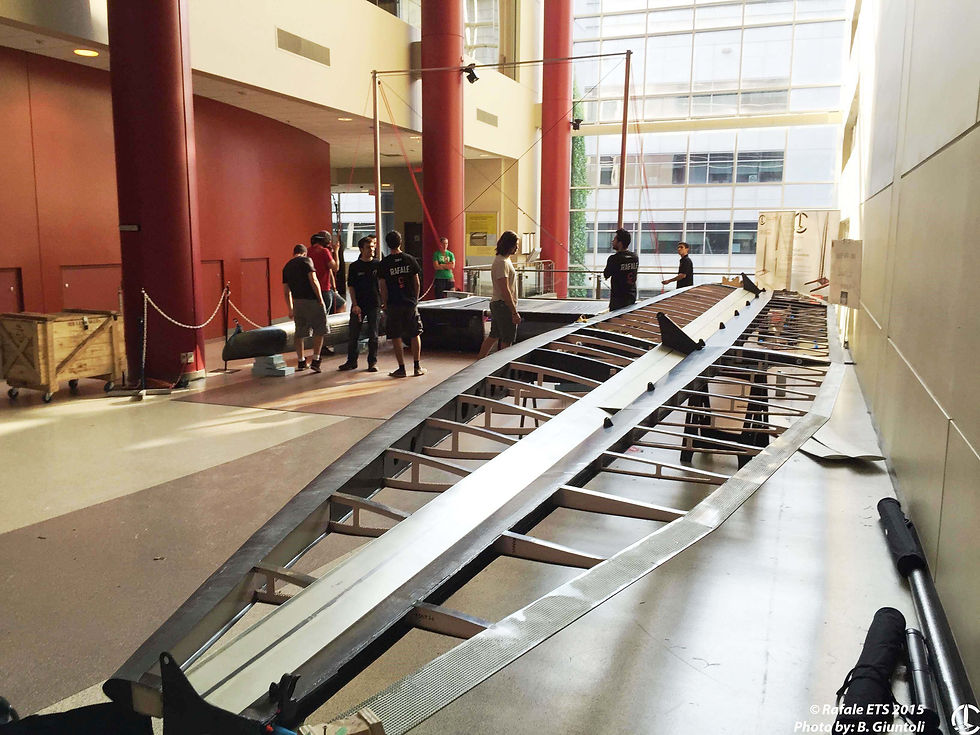



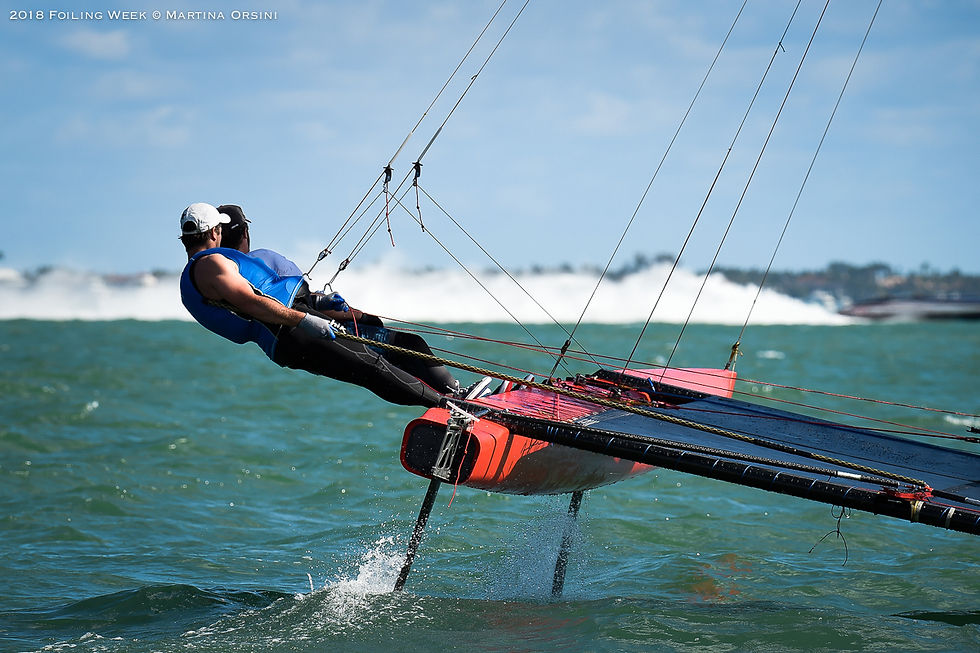
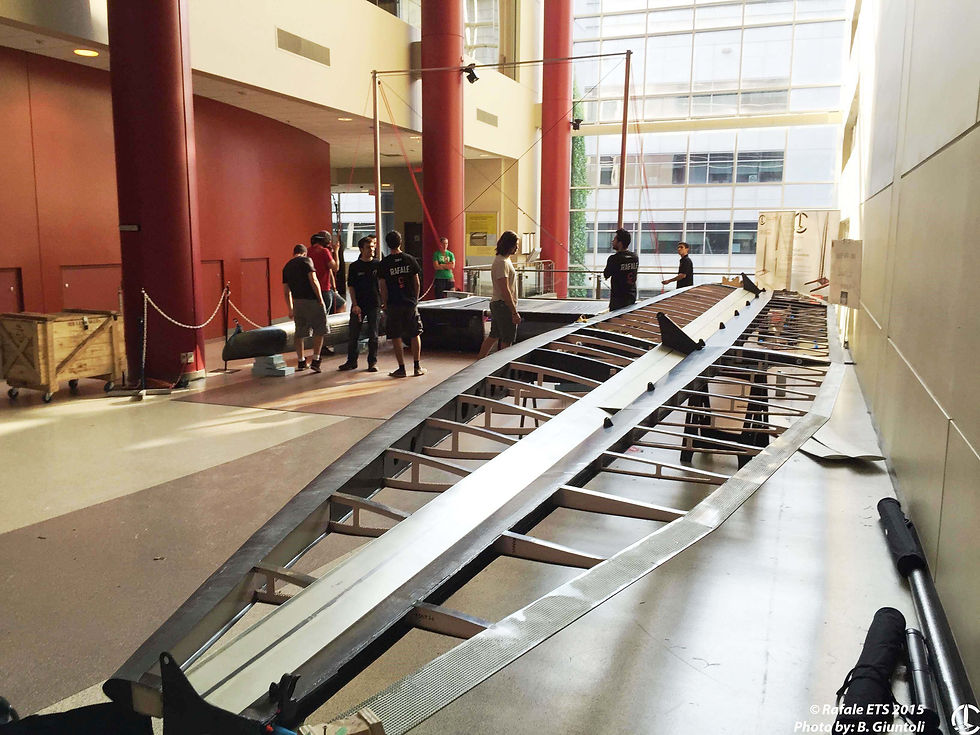



STUDENT TEAM BUILDS CARBON EPOXY C-CLASS HYDROFOIL CATAMARAN
A TEAM of 16 undergraduate and MSc engineering students from the ÉTS (École de Technologie Supérieure) in Montréal Canada has recently finished building ‘Rafale II’, an all-composite C-Class racing hydrofoil catamaran. Scott Bader provided high performance composite resin, tooling & structural adhesive products, as well as technical support.
​
Rafale II has redesigned carbon fibre epoxy prepreg hulls and cross beams, which are stiffer, 25% lighter and provide 15% more displacement volume. The speed and handling of Rafale II has also been improved by designing lighter, stronger and better performing pairs of new epoxy carbon fibre L-foil dagger boards and T-section rudder hydrofoils, which provide a higher ‘lift/drag’ ratio and greater stability when hydrofoiling.
​
The students have benefitted from the considerable support and technical advice provided from over 40 project sponsors. This includes the Canadian composites materials producer Scott Bader North America (then Scott Bader ATC), which became a key sponsor for both Rafale I and II, providing a variety of high performance composite resin, tooling and structural adhesive products, as well as technical support.
This second ETS team is building on key learnings from the Rafale I team, which made history by being the first ever student team to compete in the highly competitive and technical International C-Class Catamaran Championship (ICCCC) racing sailing competition, nicknamed the ‘Little America’s Cup’ or ‘Little Cup’. The event gained this nickname because for many years C-Class catamaran builders have been at the forefront of composite technology and design, having influenced both the creation of the World Speed Sailing Committee and modern racing yacht designs including the America’s Cup class AC72, AC45 (wingsail design) and AC50 racing catamarans.
​
Low budget high tech project challenges
During the design and production stages of Rafale I and II, in addition to the sponsors, the ETS students tackled a number of project challenges with expert support and technical advice. The key issue for Rafale I was that although the originally designed carbon fibre composite laminate used for the hulls was extremely strong, achieving a UTS of 1800 kg/cm2 in laboratory tests, it proved to be too heavy for this extreme level of competitive racing.
To reduce weight, the hull had to be totally redesigned using FEA and CAD technology based around a carbon fibre epoxy prepreg system for the new hull laminate.
The new carbon fibre epoxy prepreg hull half sections for Rafale II were moulded by low pressure vacuum bagging out of autoclave (OoA) using heated tooling with a mould dwell temperature of 93°C for 10 hours. To minimise weight, the two halves of the hull were then bonded together using Scott Bader’s Crestabond M1-30 structural adhesive in the second stage assembly process, as were the new carbon fibre cross beam sections; the beams were fabricated by ply winding onto extruded aluminium profiles using the same epoxy prepreg grade specified for the hulls.
The new L-shaped daggerboards and T-shaped rudder foil skins were moulded in the same way as the hull in two half sections using a carbon fibre epoxy prepreg, and then assembled around 3D printed cores using a structural adhesive. The assembly of the 7.62m long hull sections proved to be a real challenge for the ETS team, being the first time the students had bonded composites parts on such a large scale with no other fixings being used.
​
Fastener free assembly
Crestabond M1-30 was selected by the ETS team as the most suitable structural adhesive to bond the new epoxy carbon fibre hulls and cross beams due to a combination of its performance capabilities in use with no need for any mechanical fastenings, along with its processing characteristics, which enabled easier and quicker assembly by the team of six students compared to other adhesives trialled. Crestabond M1-30 is a toughened, two component 10:1 primer-less acrylic adhesive, developed in-house by Scott Bader for structurally bonding composites, thermoplastics and metals, designed to meet the bonding requirements of most assembly operations.
Given the extreme performance conditions that a C-Class hull has to cope with, to ensure maximum adhesion strength, the epoxy laminate bond surfaces were first sanded with 220 grade paper and then cleaned with acetone as recommended by Scott Bader; being a primer-less adhesive Crestabond products require only minimal surface cleaning of the substrates being bonded. Crestabond M1-30 was applied from 400ml coaxial cartridges using manual hand guns under 20 0C ambient conditions, which provided a 40 minute working time and a fixture time of around 85 minutes.
Crestabond M1-30 is also currently being trialled to structurally bond the new epoxy carbon hydrofoil half sections, having had some tolerance and adhesion issues with an epoxy prepreg adhesive that had been used to assemble the first set of T rudders and L-foils; once again no fastenings are used in the design.
​
Creative tooling
The MDF plugs for the new hulls and rudders were part manufactured externally by two specialist tool making companies and then finished by the ETS students, who made all the individual moulds. Poly-Fair® F24VE vinyl ester resin fairing compound, originally developed by Scott Bader North America, was used in the heated moulds for the new hull sections to cover the wire elements prior to the second mould tool infusion.
Unusually, Scott Bader’s Crestomer® 1152PA urethane acrylate based structural adhesive was also used in both the hull and the rudder and dagger boards moulds, primarily to eliminate sharp edged stress areas, especially in the thin foils and to prevent any dry areas or air inclusions in the corners during infusion; the curved radius corners also helped with fibre alignment and avoided any gelcoat displacement when the vacuum was applied during the infusion stage.
The students also found that using Crestomer 1152PA in the corners not only avoided stress concentration points in the finished parts, but being such a very tough, flexible product, had the added benefit of producing a more durable mould tool which was far less prone to corner damage during part demoulding.
As well as the structural adhesive, Scott Bader’s carbon fibre compatible Crestapol high performance urethane acrylate based resin was used extensively to manufacture key structural parts for the massive 28m2 wingsail; the leading and trailing edges, flap spars, wing foil box fairings and the bulkhead panels, were all vacuum infused using Crestapol 1250LV. The rigid bulkheads were assembled with Crestabond M1-05 and M7-05 structural adhesives, which were also used for bonding a variety of FRP and metal parts on the wingsail.
The 9.75m central carbon fibre mast, 120mm in diameter and weighing just 16kg, is the primary structural element for the wing sail, which when fully assembled provides a 13m sail height. The mast is conventionally supported by steel wire stays.
​