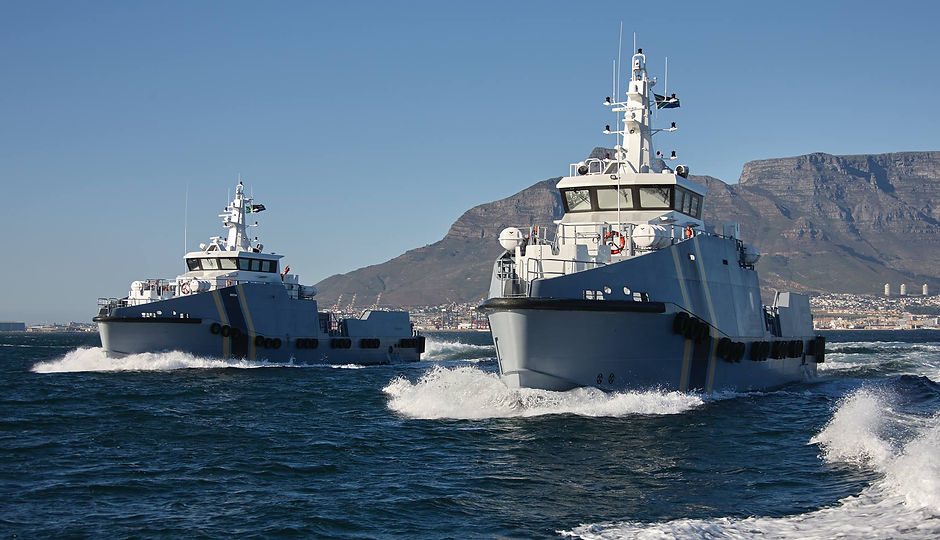.jpg)
December 2017
AMS BALLISTIC PROTECTION SOLUTION DEFENDS AGAINST PIRATE ATTACK
Photo: The 35-metre sentinels, the vessels for which AMS designed and manufactured the wheelhouses and masts before delivery to the clients in West Africa
THE true value or quality of something can only be judged when it's put to use - the results are what counts! Advanced Materials Solutions (AMS) in Stikland, Bellville in the Western Cape, recently received unambiguous evidence that their lightweight, composite ballistic protection solution for a series of wheelhouse structures installed on patrol vessels off Nigeria did just what they were supposed to – protect the crew from automatic gun fire!
AMS was commissioned to develop and construct 10 composite ballistic protected wheelhouse structures for Nautic Africa who was supplying patrol vessels to the oil industry off West Africa.
The project was completed and the wheelhouses delivered. In September one of the patrol vessels came under heavy attack from pirates. The patrol vessel suffered multiple hits, but nothing penetrated the wheelhouse structure.
Johan van Niekerk, MD of AMS said the clients were obviously very happy.
“We were also very pleased to learn that our composite solution had been so effective,” he added.
AMS will send a team to Nigeria to repair the damaged wheelhouse.
AMS is the only company in the Western Cape who have the intellectual property (IP) to manufacture components using their composite ballistic protection solution. The IP used was developed by Johan and his team at AMS over several months of trial and error, testing and more testing done at Armscor.
Johan explained that the composite ballistic protection solution AMS developed includes several layers of different composites laminated together. Using a vacuum infusion process, the protected areas of the wheelhouse were manufactured using 16mm foam on the outside with a 20mm layer inside, providing thermal and sound insulation. The ballistic protection layer – comprising specialised ceramics - is integrated into the inside layers.
For the unprotected sections of the wheelhouse, AMS used 600g/m2 glass fibre with a PVC foam skin of 55kg/m3.
“We’ve recently completed even more testing and have managed to reduce the areal density from 48kg/m2 to just 26kg/m2,” said Johan. “The same protection using steel would weigh about 70kg/m2 if 9mm Armox 500, a Swedish ballistic armour steel, was used.
The solution is certified to the STANAG Level II protection level. This means that the composite ballistic protection solution can protect against penetration by gunfire using ammunition up to 7.62x51mm NATO and includes 5.56x45mm SS109 and 7.62x39mm or AK-47 armour piercing incendiary rounds.
“When we began the project, we had absolutely nothing to work with,” explained Johan. “Through trial and error, and a lot of testing, over a period of about six months we decided on using a specific ceramic that fractures and absorbs energy, as well as developed a specialised adhesive that can resist the very high temperatures that would be caused by incendiary ammunition.”
It was a significant learning experience for the team at AMS, but one they eagerly took on and successfully achieved.